Aero Flite Trailers
"America's Smartest Trailers"
Trailer Information
Construction
Aero Flite trailers were built at the Van Nuys Metropolitan Airport in one of the same plants in which Aero Services had repaired airplanes. The construction techniques and materials used in the construction of Aero Flite trailers were identical to those used in aircraft construction. The Aero Flite trailer was designed to be very stylish, functional, aerodynamic, and light weight. Whatever vision Frederick C. Hoffman had when he designed and patented the trailer, J. Gordon Hussey and the men and women of Aero Services and Aero Lines made that vision come true in the production of Aero Flite trailers.
Conventional trailers of the late 1940s, and continuing on into modern day, were built upon a steel frame. The typical trailer had a plywood floor resting on top of the steel frame. In some cases a lower body covering called a belly pan was attached to the underside of the frame and the space between the floor and the belly pan was insulated. Aero Flite was different. A steel frame would have been more foreign to Hussey and the workers of Aero Services. They were accustomed to working with aluminum and other lightweight materials. A steel frame would have also not fit Aero Flite’s design. Aero Flite was designed to be different and Aero Flite was designed to be lightweight; therefore aluminum and magnesium were the materials of choice for constructing the frame and body.
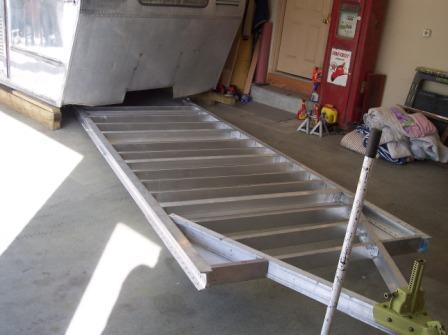
Hoffman designed the trailer as a monocoque, which means that its frame and body are unitized. The frame is insufficiently strong by itself, as is the body, but as a complete unit considerable strength and rigidity is achieved. Aero Flite’s frame is comprised of I-beam and C-channel structural members, aluminum plate, aluminum cross members, and short members extending outside the frame called outriggers. The main frame rails of the trailer are made of aluminum I-beam, approximately 4 inch high by 2 inch wide, extending from the front edge of the body to the rear of the body, where the tail of the trailer begins to cantilever. The main rails are approximately 14 feet 9 inches in length. The main rails are connected to each other via a series of cross members, to form a “ladder.” The cross members are made of aluminum sheet that has been brake-bent to form a sideways “U” shape.
By designing the front panel to be sloped, a more interesting profile was created than would have been achieved with a 90 degree angle. This design detail also provided functional benefits by increasing interior space and providing a space outside for the butane tank without requiring the tongue to be lengthened. Hoffman’s decision to slope the front panel outward also worked well with his design for a wrap around dinette seating area in the front of the trailer. The designer was able to provide seating with a comfortable seat-to-back angle instead of a less comfortable 90 degree angle, as was, and still is, common in many trailer designs. On the first several trailers, the builders created two small storage compartments at the bottom of the front panel, accessible via small hinged doors. The compartments were ingenious and blended in well to the front panels. The compartments provided storage for small tools such as the tongue jack handle and front dolly wheel. This feature has been observed on trailers with serial number 105 or below, indicating only the first few trailers had the compartments.
Flanking a large curved shatterproof front window, Hoffman utilized a set of functional louvers on the front of the trailer. The louvers, which were unique to Aero Flite, added to the space age look and feel of the trailer and gave the trailer a “high tech” look. But the louvers were designed for more than appearance reasons. They were fully functional, allowing fresh air to enter the trailer. Filters, similar to a common furnace filter, were installed inside the body between the louver openings and the interior plenum doors, filtering the air and keeping dirt and insects out of the trailer. Aero Flite was built before air conditioning systems had been devised for trailers and recreational vehicles, so Aero Flite’s filtered fresh air was a unique and welcome feature.
The cross members and rails are attached by way of angle brackets and solid aluminum rivets. The cross members and rails are also riveted to the floor, which is made of aluminum and/or magnesium. The tongue section of the frame is made from C-channel structural aluminum. The tongue rails are attached to the main rails by way of aluminum plate that is riveted to the rails. The aluminum frame and cross member components, in addition to being riveted to each other are also riveted to an aluminum or magnesium floor panel. On the early Falcons, this floor panel was made of flat aluminum plate, approximately ¼ inch thick. On later Falcons, the floor panel was made of .080 inches thick, corrugated aluminum panel, with corrugation every 6 inches across the panel. The aluminum floor panel was then covered with an impregnated paper and then balsa-core aircraft grade plywood was screwed to the aluminum floor panel. Balsa-core plywood was selected because of its comparative light weight versus conventional plywood. The use of corrugated panels on the later model Falcons provided a dead air space between the floor panel and the plywood. Aero Flite’s suspension and running gear was comprised of a single axle equipped with Warner electric brakes and 16” by 7” wide 6-ply tires. Aero Flite wheels sported a 10 inch “baby moon” style hubcap.
Careful examination of Aero Flite’s body shows some of the genius of Hoffman’s design. The trailer, which is often described as space-age looking, is also sleek and sporty and at the same time it is graceful and elegant. Hoffman designed the trailer to be both attractive and functional. The body was labor intensive to build, but was comprised primarily of panels and components the company could make in-house. Simple curves, rather than compound curves, allowed the trailers to be built without bearing the cost of expensive tooling or panel stamping. Hoffman designed the front panel so that rather than meeting the floor panel at a 90 degree angle, the panel slopes outward from the bottom up.
A new frame is installed beneath Aero Flite Falcon serial # 1078
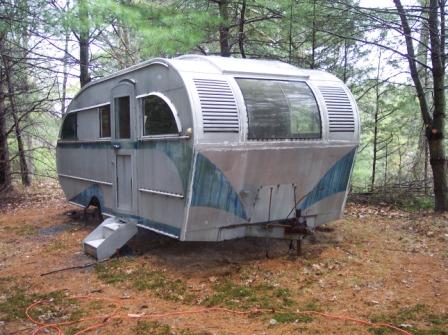
The style of roof selected by Hoffman is referred to as a clerestory roof and has a center section that extends upward, creating additional headroom and improving airflow. The roof had one or two ventilators, depending on when it was built, to allow hot air to exit and fresh air and sunlight to enter from above. The center section of the roof panel did not follow the side profile of the trailer but instead leveled off at the rear, creating a dorsal fin appearance on the outside and plenty of headroom on the inside. At the point where the roof met with the rear body, above a large window in the center of the rear body, the trailer featured a hinged vent mechanism, operable from inside the trailer. This rear vent was part of Hoffman’s design for creating cross-ventilation using the front louvers to draw in cool air and exhausting heated air through the roof vents and rear vent.
No one knows if Hoffman designed the trailer by first developing the shape of the body or if Hoffman started with a floor plan layout and worked from the inside out. In designing Aero Flite Hoffman achieved three objectives, each of which challenged many trailer designers of the day; Hoffman created a trailer that was unusual and interesting to look at, lightweight and efficient to tow, and elegant and comfortable on the inside. Hoffman did not compromise on the inside for a particular look on the outside, or vice versa. The exterior design and interior design fit each other and worked well together to create a trailer Aero Lines billed as “America’s Smartest Trailer.”
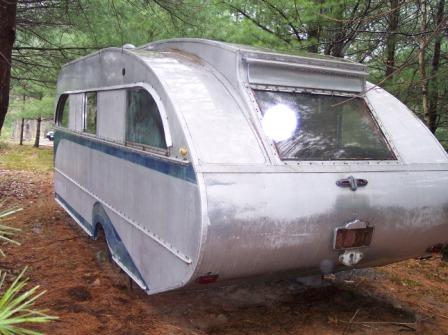
The trailer’s rear body area showed another example of Hoffman’s ability to create an attractive and unique appearance on the outside in a way that was highly functional on the inside. The rear body section was cantilevered, with more than 36 inches of body extending beyond the rear of the trailer’s frame. This section housed the bed; therefore, foot room and headroom were unimportant, as occupants would not be standing in this area of the trailer. The cantilevered effect added usable space inside the trailer without the need to square off the rear end of the trailer. In his design of the trailer’s roof, Hoffman again used clever and careful design to create an interesting look while improving comfort for Aero Flite’s occupants.
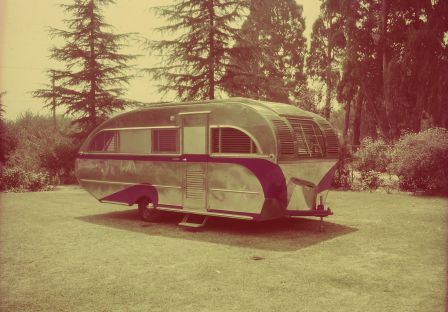
The sides of Aero Flite trailers were constructed of flat panel aluminum. The aluminum alloy for all the exterior panels was 2024 T3 and the panels were 40 thousandths of an inch thick (.040 inches). Early models, such as the one pictured at right, had side panels that were completely flat. Later models, primarily late 1948’s, used flat panels that contained sheet metal brake marks, or horizontal “runs,” every 6 inches to add ornamentation and texture. The runs would have also added some degree of increased rigidity to the aluminum panels.
Hoffman broke up the vastness of the side panels and added protection for the large side panels by making use of rub rails that ran the length of the trailer. The flat panel trailers had three sets of rub rails and those with horizontal runs had two sets of rub rails. If the trailer was towed too close to another vehicle or stationary object, the rub rails would sustain damage before the body would be impacted. The sides of the trailers were broken up through the use of three windows per side and an entry door on the trailer’s curb side. Hoffman designed the shape of the front and rear side windows as mirror copies of each other, adding symmetry and balance at the midsection of the trailer. The front side windows were stationary and did not open. The center and rear side windows were designed as pocket windows. The center window was opened by sliding its glass pane to the rear of the trailer where it disappeared into the wall. The rear side window was opened by sliding its glass pane forward, into the wall. Each window was equipped with a Lucite hand grip, affixed to the glass pane. A latch mechanism inside the trailer allowed the windows to be locked from the inside. Aero Flite used textured polished aluminum between the window openings and door panel. The door itself was hinged from the right, opening toward the front of the coach. This was a slight deviation from Hoffman’s original drawing, which showed the hinges on the left side of the door. A set of louvers, similar in design to those on the front panel, were installed in the lower half of the door and late 1948 models featured a porthole style window in the door. The side of the trailer was accentuated by a teardrop shaped wheel opening.
Pilot trailer, serial number 101X, as found, 2006
An early advertising photo. Photo credit: University of Nevada
IMPORTANT NOTE: All content on this website is owned by Kevin Reabe and is copyright protected.
Company History
Trailer Information
Other Information